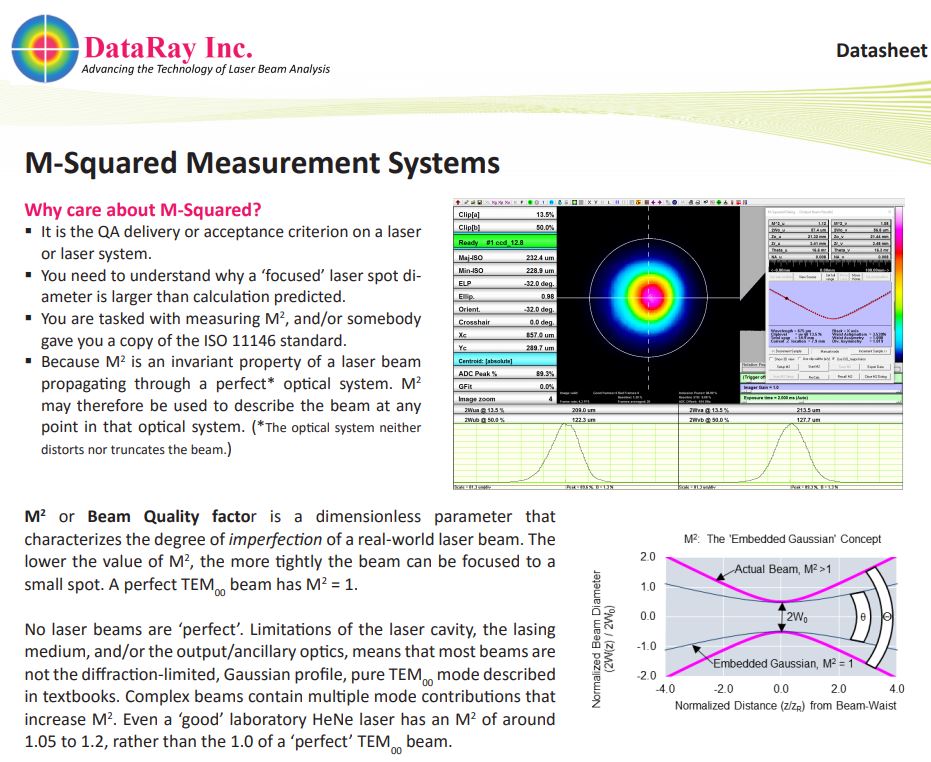
M-Squared Measurement Systems
Why care about M-Squared? It is the QA delivery or acceptance criterion on a laser or laser system. You need to understand why a ‘focused’ laser spot diameter is larger than calculation predicted. You are tasked with measuring M2 , and/or somebody gave you a copy of the ISO 11146 standard. Because M2 is an invariant property of a laser beam propagating through a perfect* optical system. M2 may therefore be used to describe the beam at any point in that optical system. (*The optical system neither distorts nor truncates the beam.)
M2 or Beam Quality factor is a dimensionless parameter that characterizes the degree of imperfection of a real-world laser beam. The lower the value of M2 , the more tightly the beam can be focused to a small spot. A perfect TEM00 beam has M2 = 1. No laser beams are ‘perfect’. Limitations of the laser cavity, the lasing medium, and/or the output/ancillary optics, means that most beams are not the diffraction-limited, Gaussian profile, pure TEM00 mode described in textbooks. Complex beams contain multiple mode contributions that increase M2 . Even a ‘good’ laboratory HeNe laser has an M2 of around 1.05 to 1.2, rather than the 1.0 of a ‘perfect’ TEM00 beam.
At its simplest M2 may defined as: The ratio of the divergence of the actual beam, to that of a theoretical, diffraction-limited beam with the same waist diameter.
ISO 11146 Compliant, Single Plane Measurement Systems on a Moving Stage
The ISO 11146 standard requires measurement of the second moment beam diameter in multiple planes (≥5) about the beamwaist and multiple planes (≥5) in the far field. In most circumstances this requires a single plane beam profiler moved along the propagation axis by a z stage.